Термическая и химико-термическая обработка
Термическая обработка
Термическая обработка позволяет улучшить свойства металлов и сплавов, не изменяя химический состав металла.
Обычно термически обрабатывают детали на начальном или конечном, а иногда и промежуточных этапах подготовки. Термическая обработка производится с целью размягчения или укрепления заготовки. У каждого вида металла существует своя собственная температура термического воздействия, соответственно и виды термообработки тоже различны.
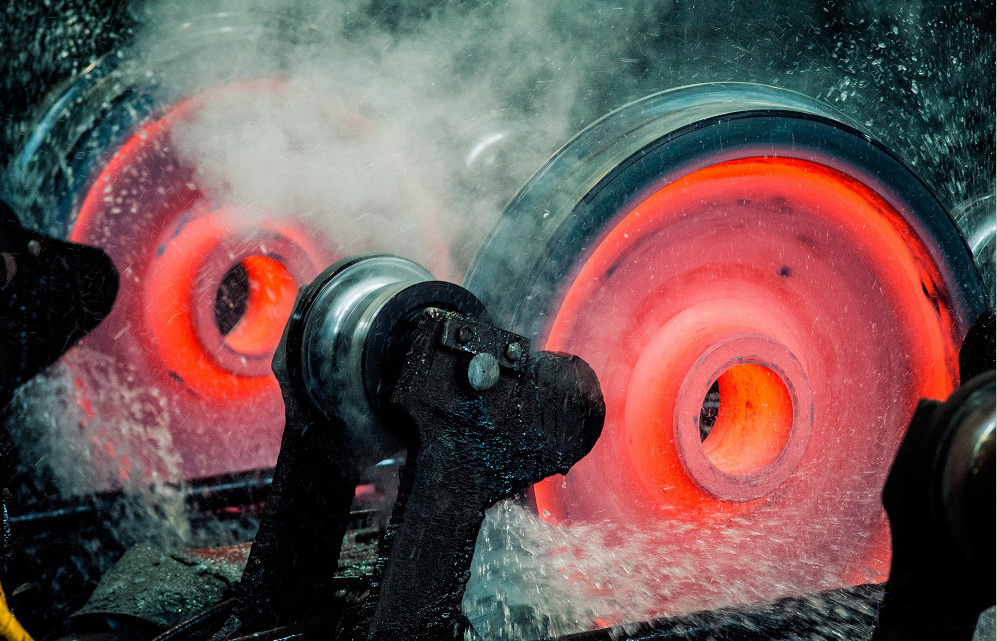
Виды термообработки
Термообработка делится на четыре вида:
- отжиг;
- закалка;
- отпуск;
- нормализация.
Отжиг используют если возникает необходимость в снижении твердости заготовки, а также в придании ей легкости. После отжига металл становится менее напряженным и более однородным. Охлаждается в печи.
Закаленный металл становится тверже, но одновременно с этим и более хрупким.Если выполнить закалку несколько раз, металл теряет пластичность и вязкость.
Отпуск применяется для увеличения пластичности делали и уменьшения хрупкости, прочность металла при этом остается практически без изменений.
Нормализация — термическая обработка, схожая с отжигом. Различия этих термообработок состоит в том, что при нормализации сталь охлаждается на воздухе.
Химико-термическая обработка
Химико-термическая обработка - совокупность операций термической обработки с насыщением поверхности изделия различными элементами (углерод, азот, алюминий, кремний, хром и др.) при высоких температурах.
Химико-термическая обработка повышает твердость, износостойкость, коррозионную стойкость. Химико-термическая обработка, создавая на поверхности изделий благоприятные остаточные напряжения сжатия, увеличивает надежность, долговечность.
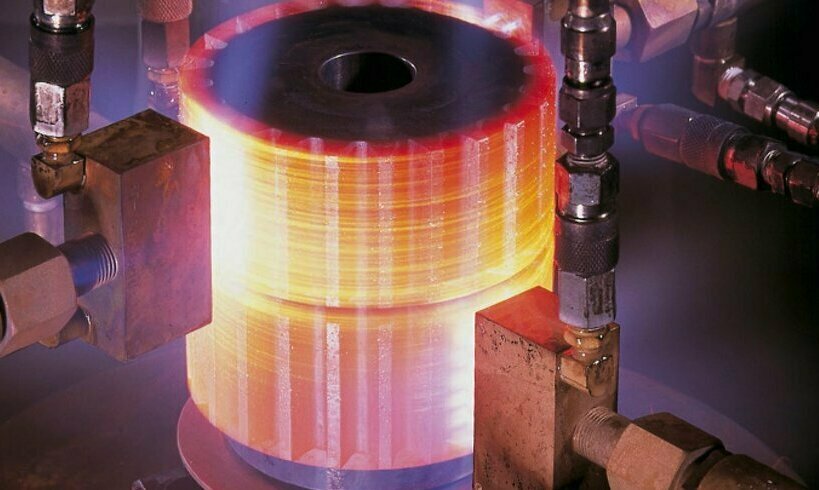
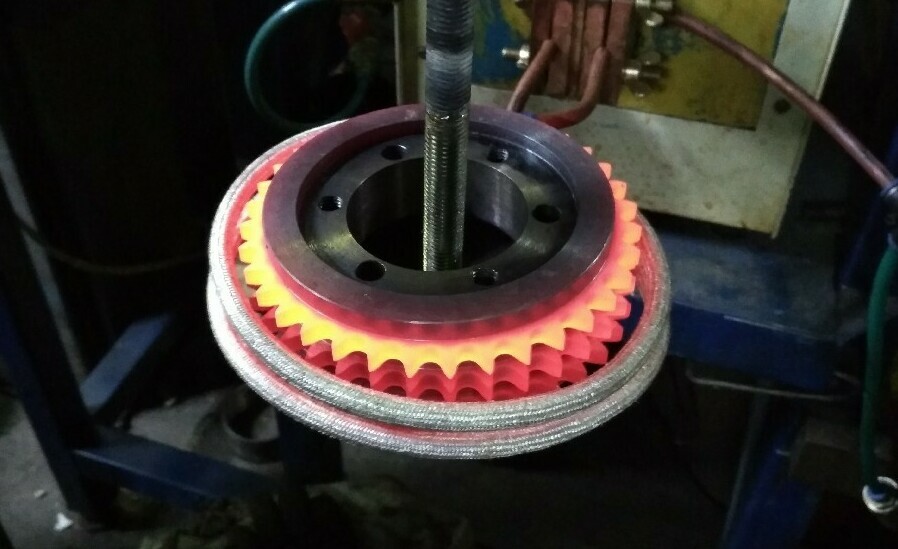
Цементация
Цементация - химико-термическая обработка, заключающаяся в диффузионном насыщении поверхностного слоя атомами углерода при нагреве до температуры 900…950С.
Цель цементации - обогатить поверхностный слой детали углеродом до концентрации 0,8—1,1% и получить, после закалки, высокую твердость поверхностного слоя при сохранении пластичной сердцевины, что обеспечивает выносливость изделия в целом при изгибе и кручении.
Азотирование
Азотирование - процесс насыщения поверхностного слоя детали азотом, с целью повышения твёрдости, износоустойчивости, предела усталости и коррозионной стойкости.
Азотирование проводится при 500-600 °С в герметично закрытом контейнере из железа, который внедряется в печь. В контейнер закладывают детали, которые будут подвержены азотированию.
Туда же под давлением запускается аммиак, который под действием высоких температур распадается на водород и атомарный азот. По окончании процедуры печь плавно охлаждается вместе с потоком аммиака. Деталь получает высокую твердость.
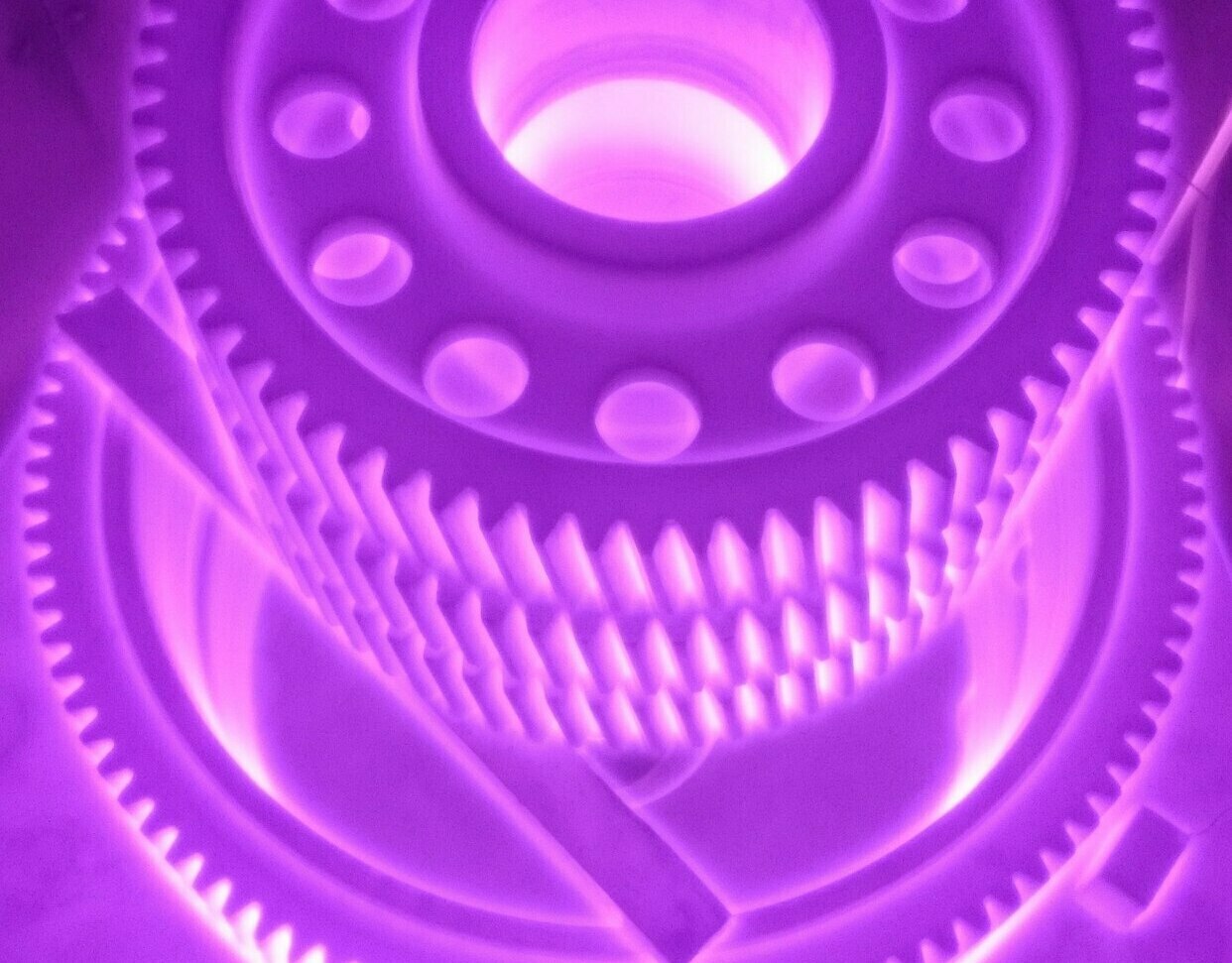
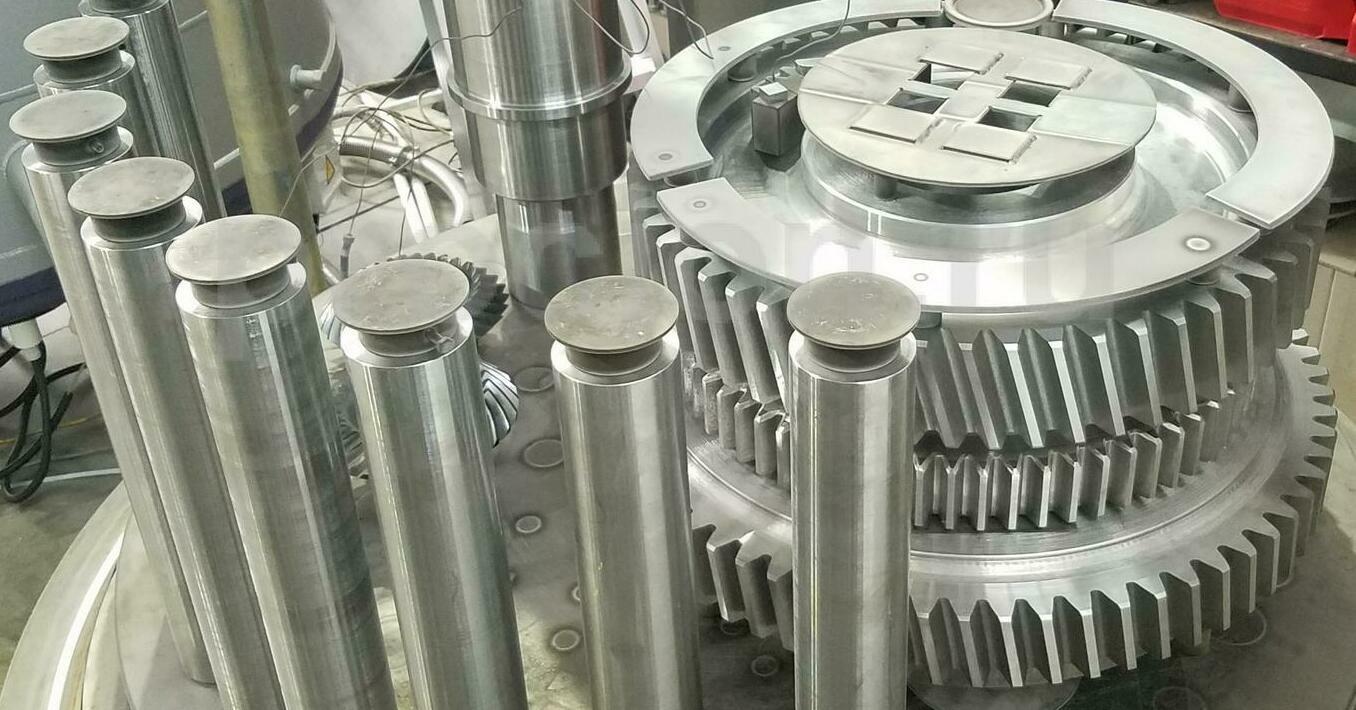
Преимущества азотирования
Твердость углеродистой стали после азотирования составляет 200..250 HV
Твердость легированной стали 600..800 HV
Для сталей, имеющих в своем составе алюминии, хром и молибден, твердость составит от 1200 HV и выше.
Одновременно с тем, как твердость посредством легирующих элементов становится выше, толщина азотированного слоя – ниже
Нитроцементация (цианирование)
Нитроцементация (цианирование) - химико-термическая обработка с одновременным поверхностным насыщением изделий азотом и углеродом при повышенных температурах с последующими закалкой и отпуском для повышения износо- и коррозионной устойчивости, а также сопротивлению усталости. Нитроцементация может проводиться в газовой среде при температуре 840..860°С - нитроцианирование, в жидкой среде - при температуре 820…950°С - жидкостное цианирование в расплавленных солях, содержащих группу NaCN.
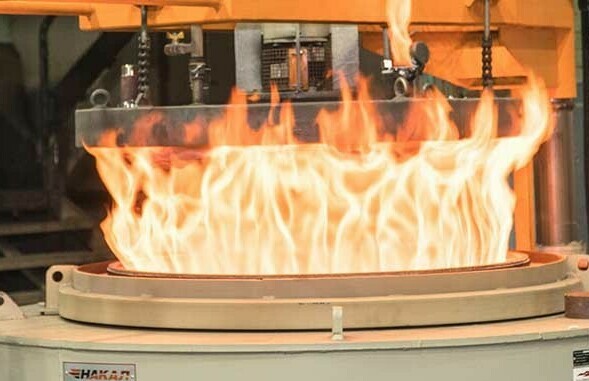